The Therapeutic Goods Administration (TGA), an Australian regulating authority in the sphere of healthcare products, has published a guidance document dedicated to the classification of active medical devices (including software-based ones). The document issued in October 2021 constitutes the initial version of the guidance. The document is intended to provide additional clarifications and recommendations to be considered by medical device manufacturers in determining the appropriate class of the devices they are going to place on the market.
The authority additionally emphasizes that the present guidance is not exhaustive and does not cover any classification rules for medical devices. Hence, it is the sole responsibility of the manufacturer to familiarize themselves with the applicable legislation in terms of the classification of medical devices.
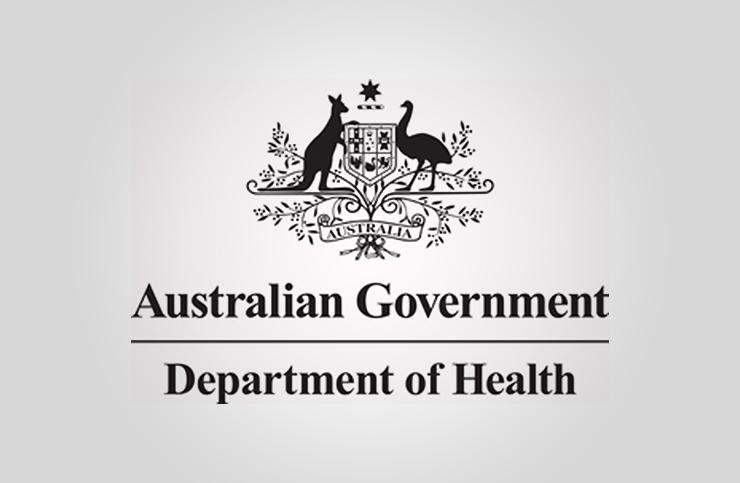
Table of Contents
Regulatory Background
According to the applicable legislation, all medical devices are divided into four classes depending on the significance of harm they could potentially cause, namely:
- Class I (lowest classification);
- Class IIa;
- Class IIb;
- Class III (highest classification).
The authority states that the regulatory requirements to be applied depending on the class of a medical device in question under the current classification system. In particular, the class of the device should be taken into consideration when determining the conformity assessment procedures the device should be subject to be allowed for marketing and use in Australia. It is important to mention that according to existing legislation, any medical devices intended to be supplied in the country are subject to inclusion in the Australian Register of Therapeutic Goods (ARTG), a country’s register of healthcare products subject to regulatory oversight.
The TGA guidance further defines an active medical device, which is the one initially intended to perform its functions by converting the energy from the appropriate source, provided it is not intended to transmit energy. The authority also states that software-based medical devices are active medical devices, including software that is a medical device itself and medical devices that incorporate software. It is also important to mention that the scope of the present guidance does not cover in vitro diagnostic medical devices.
Classification Process: Key Points
According to the TGA guidance, the classification rules to be applied are set forth by Schedule 2 (Part 4) of the Therapeutic Goods (Medical Devices) Regulations 2002 (the Regulations). These rules are based on the core principles to be considered when determining the class of the device under the current classification. These principles include the following ones:
- If a medical device is designed to be used in combination with another medical device, each of the devices is classified separately;
- An accessory to a medical device is classified separately from the medical device; and
- If a medical device is driven, or influenced, by an item of software, the software has the same classification as the medical device.
Under the general rule, the initial classification of a new medical device should be performed by its manufacturer. As it was mentioned before, the particular regulatory requirements the device shall be subject to will be further determined depending on the class of the device.
Applying the Classification Rules
The guidance further describes the particular way classification rules should be applied when determining the class of a new medical device. According to the guidance, such a determination should be based on the intended purpose of a medical device, and also on the way it operates. When determining the class of a device, the manufacturer should take into consideration any classification rules the device could be subject to. The authority additionally emphasizes that in situations when several rules could be applied, the one prescribing the highest class should be applied. In the case of complex medical devices with numerous functions, it is important to evaluate each of them separately. The class of a medical device, in general, should be determined by the highest class of any of its functions.
The TGA mentions that medical devices that are intended solely to be exported outside Australia should be classified as Class I medical devices.
Another important aspect relates to changes to the functionality of medical devices. According to the guidance, in case of any changes to the existing medical device, the manufacturer should duly review the classification to ensure its applicability. According to the guidance, the changes to a medical device that could potentially require changes in classification are the changes to:
- The intended purpose or indications for use;
- The functionality of the device (adding new functions or removing existing ones);
- The claims were made by the manufacturer about the device.
The document further provides references to the appropriate classification rules related to recording patient images, anatomic models, diagnosis, screening, monitoring, investigation of the anatomy or physiology, specifying or recommending treatment or intervention, and therapy.
Implantable Devices
One of the rules described in the guidance applies to active implantable medical devices and implantable accessories thereto. The scope of the rule also covers the devices intended to be used to control or monitor the operations of another active implantable device.
The authority also emphasizes that starting from November 25, 2021, the approach to the classification of active implantable devices would be subject to changes. In particular, such devices would be reclassified from Class AIMD as a special category for these products to Class III – the highest class under the applicable risk-based classification. According to the applicable classification rules, any devices falling within the scope outlined here above should be assigned to Class III.
General Classification Rule
Apart from device-specific classification rules, there is a general rule to be applied to the devices falling outside the scope of any other classification rules. According to this rule, such devices should be classified as Class I medical devices. Examples of such devices include examination lights; surgical microscopes; dental curing lights; and surgical microscopes with recording functionality.
In summary, the present TGA guidance provides an overview of an existing regulatory framework in the sphere of classification of medical devices and highlights the most important aspects to be taken into consideration by medical device manufacturers when determining the class of a medical device they are going to place on the market. The document also describes in detail device-specific classification rules to be applied depending on the intended purpose of a medical device in question and the way it operates.
Sources:
How Can RegDesk Help?
RegDesk is a next-generation web-based software for medical device and IVD companies. Our cutting-edge platform uses machine learning to provide regulatory intelligence, application preparation, submission, and approvals management globally. Our clients also have access to our network of over 4000 compliance experts worldwide to obtain verification on critical questions. Applications that normally take 6 months to prepare can now be prepared within 6 days using RegDesk Dash(TM). Global expansion has never been this simple.