The article provides an overview of the existing regulatory framework for submissions related to healthcare products.
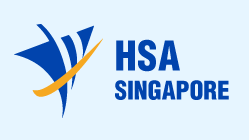
Table of Contents
The Health Services Authority (HSA), Singapore’s regulating authority in the sphere of healthcare products, has published a guidance document dedicated to product registration submissions. In particular, the document describes in detail the approach to be applied in the context of E-Submissions. It is important to mention that the provisions of the guidance are non-binding in their legal nature and are not intended to introduce new rules or impose new obligations, but rather to provide additional clarifications and recommendations to be taken into consideration by medical device manufacturers and other parties involved in order to ensure compliance with the respective regulatory requirements. The authority also reserves the right to make changes to the guidance and recommendations provided therein, should such changes be reasonably necessary to reflect corresponding amendments to the underlying legislation. The present document constitutes a second revision of the guidance.
Regulatory Background
According to the document, it is intended to provide guidance on the submission of a product registration dossier to HSA via the Medocumentation, Information, and Communication System (MEDICS). In particular, the document provides clarifications with respect to specific modules to be used.
Under the general rule, the applications for product registration should be submitted online in electronic format in accordance with the ASEAN Common Submission Dossier Template (CSDT) or in line with the recommendations developed by the International Medical Device Regulators Forum (IMDRF) for general medical devices.
Application Form: Key Points
According to the guidance, the technical dossier describing the product in question, together with all the necessary supporting documentation, should be submitted online using the “Dossier & Supporting Document(s)” section of the application form available via the aforementioned submission system. The authority mentions that several modules should be used when completing the application form. The HSA additionally emphasizes the importance of ensuring the application form is filled in properly,and all the documents are named and attached properly in order to facilitate and streamline the review of the application.
As further explained by the authority, the responses to the questions raised in the course of the assessment process should be provided in writing. Should the response be accompanied by any additional documents, such documents should be named accordingly in order to ensure their proper identification.
Depending on the particular regulatory framework the product in question is subject to, the scope of documentation provided when applying for registration shall include:
- Letter of authorization,
- List of Configurations,
- Proof of reference agency’s ,
- Proof of marketing history in the reference agencies’ jurisdictions (e.g., invoice with date, proof of sale or a declaration on marketing history),
- Declaration of no safety issues globally,
- Executive summary covering, inter alia, the following:
- Introductory descriptive information on the medical device, the intended use and indications for use of the device,
- Information on the use of the device, if any, such as targeted patient population, user profile, specific disease status or clincal condition, mode of action, etc.,
- If the medical device has any unique or novel feature or characteristic, a description must be provided.,
- Any high-level background information or details that the product owner wishes to highlight in relation to the device, its history or relation to other approved devices,
- List of countries from HSA’s reference regulatory agency, jurisdictions where the medical device is marketed,
- Date and country where the device was first introduced for commercial distribution, globally,
- Registration status and approved intended use and indications of the medical device in HSA’s recognised agencies
- Decoration from product owner that the labeling, packaging and IFU of the device for sale in Singapore are identical or not identical to that approved by reference agency being used as the basis for evaluation route,
- If the subject device is different in any way from those approved by the reference agencies, the differences should be described.
Apart from the above, the medical device application form should also include details on the adverse events related to the device in question that meet the reporting threshold, as well as any and all Field Safety Corrective Actions (FSCA) taken in order to ensure the safety of patients worldwide. In the event that some of the corrective actions remain open at the time of submission, the applicant is expected to provide a detailed description of the actions taken and the appropriate justification. Should there be no adverse events subject to reporting or FSCAs related to the product in question, the appropriate attestation letter should be issued by the party responsible for the product.
Essential Principles
The guidance also provides recommendations related to the Essential Principles and the way they should be referred to in medical device applications. In particular, the authority expects the applicant to include an Essential Principles conformity checklist. It is important to mention that the applicant may demonstrate conformity not only to the Essential Principles adopted in Singapore but also to the ones applicable in the EU or Australia. Other than that, the applicant should also provide a Declaration of Conformity as well as a list of applicable standards the product complies with in terms of design and manufacture.
In summary, the present HSA guidance provides a brief overview of the regulatory requirements for application forms to be submitted when applying for medical device registration in Singapore. The document also outlines the scope of general information and documentation to be submitted by the applicant in order to ensure the completeness of the submission and facilitate its subsequent review by the authority.
How Can RegDesk Help?
RegDesk is an AI-powered Regulatory Information Management System (RIMS) designed to simplify global compliance for medical device companies. With regulatory intelligence covering 120+ markets, RegDesk helps you prepare and publish global submissions, manage standards, conduct impact assessments, and stay ahead of regulatory changes all from a single, centralized platform. Expanding into new markets has never been easier.