The new article describes in detail the aspects related to different types of MRI safety labelling to be used to indicate the safety status of the device intended to be marketed and used in the US.
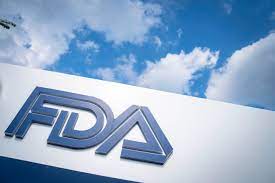
Table of content
The Food and Drug Administration (FDA or the Agency), the US regulating authority in the sphere of healthcare products, has published a revised guidance document dedicated to testing and labelling medical devices for safety in the magnetic resonance (MR) environment.
The document provides an overview of the applicable regulatory requirements, as well as additional clarifications and recommendations to be taken into consideration by medical device manufacturers and other parties involved to ensure compliance thereto.
At the same time, provisions of the guidance are non-binding in their legal nature, nor are they intended to introduce new rules or impose new obligations.
The authority also explicitly states that an alternative approach could be applied, provided such an approach is in line with the existing legal framework and has been agreed with the authority in advance.
MRI Safety Labeling
As per the applicable legislation, when submitting a medical device for premarket approval, it’s mandatory to include comprehensive labelling that meets the requirements specified under 21 CFR 807.87(e) or 21 CFR 814.20(b)(10), as well as all relevant FDA labelling requirements, such as those set forth by 21 CFR part 801.
This labelling must provide healthcare professionals with the necessary details to ascertain the device’s safety within an MR environment.
MRI Safety Information Section
As further explained by the FDA, a dedicated section titled “MRI Safety Information” should be present in the labelling, ideally listed in the table of contents for easy reference.
The device must be classified as MR Safe, MR Unsafe, or MR Conditional based on an assessment of its safety in the MR environment.
The labelling should incorporate the applicable symbol from ASTM F2503, favouring colour symbols but allowing for black-and-white versions.
This information should be readily accessible, possibly through the manufacturer’s website or a customer service telephone line, ensuring the device is clearly and unambiguously identified.
Definitions and Designations
The document also describes in detail the main terms and concepts used in the context of MRI safety labelling.
- MR Safe devices are inherently nonmagnetic, nonmetallic, and electrically nonconductive (with conductivity less than 2 S/m).
Materials like most plastics, glass, and ceramics typically fall into this category, and a scientific rationale can often justify the MR Safe designation without the need for additional testing to be conducted. - MR Conditional devices may contain metal, such as small metallic markers or metal-containing polymers, which necessitates certain conditions for safe MR environment entry. Labelling should be based on a scientific rationale or testing.
- MR Unsafe devices are those that should not enter the MR environment due to the presence of electrically conductive components, potentially causing harm.
Healthcare Provider and Patient Information
According to the recommendations provided in the guidance, the labelling used should appeal to a broad audience, including the implanting healthcare provider, the provider overseeing ongoing care, and the one prescribing the MR exam.
For devices labelled as MR Conditional, there should be clear instructions on the conditions required for safe MR operation, which may restrict the availability of some MR procedures.
Device Identification and Safety Status
The document further distinguishes two types of labelling:
- Healthcare provider labelling should unequivocally identify the device and its MR safety status (Safe, Unsafe, Conditional).
If MR Conditional status applies, the specific conditions for safe use must be detailed. - Patient labelling should also clearly identify the device and its MR safety status. For MR Unsafe devices, patients should be warned not to undergo MR examinations with the device implanted or attached.
MR Conditional devices require patients to consult their healthcare provider before an MR exam and notify MRI personnel of the device’s presence and conditions for safe use.
Content and Format for Labeling
Each safety category (Safe, Unsafe, Conditional) has specific recommendations for content and labelling format.
For instance, MR Safe devices should be labelled without unnecessary details, MR Unsafe devices should carry warnings about being kept out of the MR environment, and MR Conditional devices should list the conditions under which they can safely enter the MR environment.
Labelling should also include a comprehensive list of conditions for safe use, such as permissible magnetic field strengths, types of RF field exposures, and any necessary instructions before or after an MR exam.
Information on image artifacts caused by the device should also be included, along with any additional instructions essential for safe MR use.
For MR Conditional devices that remain outside the MR system bore, labelling should provide conditions for the safe use of the static magnetic field and include any necessary warnings about projectile hazards or equipment operation effects.
Safety Not Evaluated
The document also describes the approach to be applied when the product in question has not undergone a proper safety evaluation.
According to the guidance, in cases where a device has not been evaluated for safety in the MR environment, a specific labeling statement is recommended, explaining the absence of safety testing and the potential risks of MR exams with such devices.
This labeling should not be used if the device is known to have adverse effects in the MR environment, is typically labeled as Unsafe or Conditional, or if it contains ferromagnetic material, is an active device, or is partially implanted.
For devices where MRI safety has not been established, manufacturers should consider a pre-submission to the FDA for guidance before making a regulatory submission.
Conclusion
In summary, the present guidance outlines the main types of MRI safety labeling and highlights the key points to be considered when placing each of them. The document also provides clarifications on the way of action in case there was no MR safety assessment conducted.
How Can RegDesk Help?
RegDesk is an AI-powered Regulatory Information Management System (RIMS) designed to simplify global compliance for medical device companies. With regulatory intelligence covering 120+ markets, RegDesk helps you prepare and publish global submissions, manage standards, conduct impact assessments, and stay ahead of regulatory changes all from a single, centralized platform. Expanding into new markets has never been easier.