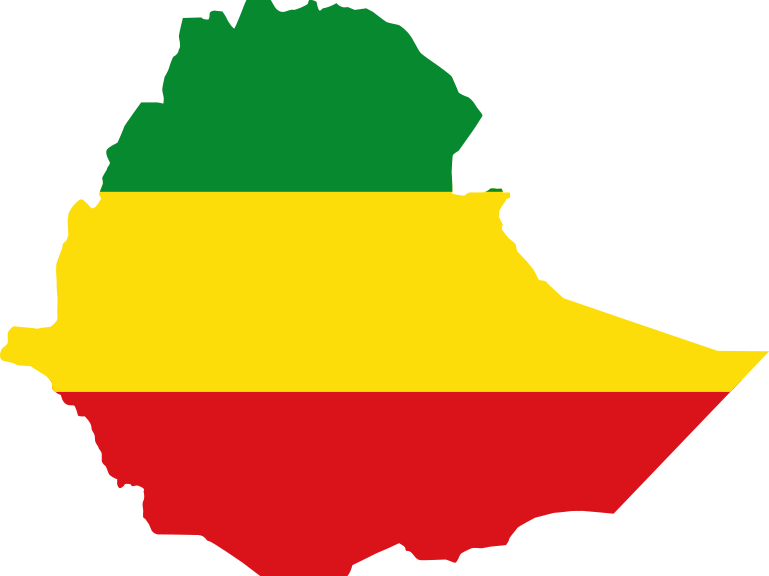
Table of Contents
General Principles
First of all, the authority mentions that the level of regulatory scrutiny to be applied will be determined based on the risks associated with a medical device in question when used for its intended purpose. Thus, the party interested in placing a medical device on the market should analyze the applicable regulatory framework to identify the requirements the device should be subject to and follow the proper pathway. Such an approach allows to reduce the unneeded regulatory burden, and also streamline and accelerate the procedures associated with placing medical devices on the market to make new medical devices available to patients and customers while ensuring any products meet the applicable safety and performance requirements and standards.
To assist medical device manufacturers, the authority describes the general principles to be followed concerning the submission process, namely:
- Product Dossier Clarity and Completeness. According to the first principle, the application to be submitted by an interested party should contain all the information necessary for the authority to assess the safety and effectiveness of a product in question. When completing the submission dossier, an applicant should consider the recommendations provided in this guidance, and also in other device-specific guidance documents, when applicable. Failure of an applicant to provide all information required could lead to additional delays or even rejection of the application. The information should be provided in a clear and structured way, otherwise, the authority reserves the right to reject the submission. The documents submitted should contain clear references, and all the statements and claims should be supported by the respective evidence.
- Applicability of Supporting Evidence to the Product under review. As it was mentioned before, all claims the manufacturer makes should be based on solid evidence collected by the manufacturer in the course of the appropriate investigations. The authority additionally emphasizes the importance of ensuring that all the studies conducted to assess the safety and performance of the product and collect necessary evidence correspond to the intended use of the medical device subject to review, and also the environment the product is intended to be used in. The document states that the manufacturer shall provide the appropriate technical specifications and the minimum safety and performance requirements that shall be met by a product to ensure that it is safe and performs optimally.
General Common Requirements
Apart from the general principles outlined hereinabove, the document also describes the general common requirements for different types of applications. In particular, the authority describes the elements of the submission dossier and highlights the key points to be considered about each of the elements. According to the guidance, an application for medical device marketing authorization should contain, inter alia, the following components:
- Application form containing all necessary information about the product in question and its manufacturer as prescribed by the appropriate template.
- An application letter is a document to be used in case the application for marketing authorization is submitted by another entity on behalf of the manufacturer (license holder). By providing such a letter, a license holder authorizes the local representative to act on its behalf when applying for registration for placing the product on the market. It is important to mention that each manufacturer (license holder) may appoint only one local agent concerning a single medical device.
- Agency agreement – a contract foreign manufacturer shall conclude with its local representative. The document should outline the spheres of responsibility of both parties and govern the relationship between them. The authority also mentions that foreign manufacturers may appoint more than one local agent to market their products in the country. The scope of the agreement should also cover the responsibilities of the parties in the sphere of post-market surveillance and reporting. The minimum validity period for such an agreement should be one year. The authority additionally emphasizes that the agent representing the manufacturer for importation should hold a license issued by the ministry of trade and a certificate of competence issued by the Authority at the time of importation of the product. The guidance also provides a template of the said agreement.
In certain cases, a three-party agreement may take place – for instance, in case the parties involved include the manufacturer, supplier, and local agent. Alternatively, there could be two separate agreements between the respective parties. As in the case with local agents, the supplier should also hold a valid establishment license confirming that it is entitled to undertake the appropriate activities.
Service Fee for Registration of Medical Devices
The document also provides clarifications regarding the fee payable by an interested party for the registration of a medical device intended to be marketed in Ethiopia. The authority states that an application should be accompanied by the receipt of service fees paid by the applicant following the Rate of Service Fees issued by Council of Minister Regulation No. 370/2015 depending on the category of application.
According to the current version of the said regulation, the payable fees should be the following:
- New Application Screening – 350 birrs;
- New Application Evaluation – 1300 birr;
- Laboratory Test – 200 US dollars;
- Renewal Application Evaluation – 870 birrs;
- Major Variation Application Evaluation – 870 birrs;
- Minor Variation Application Evaluation – 650 birrs;
- Agency Agreement – 50 US dollars.
The authority additionally emphasizes that in all cases the application fee should be paid before the application is submitted or at the time of submission.
In summary, the present EFDA guidance describes the general principles to be followed when applying for marketing authorization concerning the content of the submission and the way the information should be provided and also provides clarifications regarding the main elements of the submission dossier that are common for all types of submissions. Apart from this, the document provides information about the fees and the way they should be paid.
Sources:
How Can RegDesk Help?
RegDesk is a next-generation web-based software for medical device and IVD companies. Our cutting-edge platform uses machine learning to provide regulatory intelligence, application preparation, submission, and approvals management globally. Our clients also have access to our network of over 4000 compliance experts worldwide to obtain verification on critical questions. Applications that normally take 6 months to prepare can now be prepared within 6 days using RegDesk Dash(TM). Global expansion has never been this simple.